BASF Report 2021 Management’s Report – Energy and Climate Protection 130 Specific greenhouse gas emissions and energy efficiency Certified energy management systems (ISO 50001) at BASF Group sites Carbon footprint, product carbon footprint and climate worldwide, in terms of primary energy demand protection products Energy use and greenhouse gas emissions are closely linked to % capacity utilization and production volumes at our plants. Specific 85.1 91.0 90.2 BASF has published a comprehensive corporate carbon footprint greenhouse gas emissions in 2021 amounted to 0.564 metric tons 69.9 every year since 2008. This reports on all emissions along the value 1 of CO equivalents per metric ton of sales product, a decrease of chain – from raw materials extraction to production and disposal. 2 54.3 11.7% compared with the previous year (2020: 0.639 metric tons of 42.3 CO2 equivalents per metric ton of sales product). This was mainly The Scope 3 greenhouse gas emissions arising before and due to higher demand compared with the previous year and conse- after BASF’s activities in the value chain (in accordance with the quently, better and more stable capacity utilization at our plants. In Greenhouse Gas Protocol’s definition) were determined as around addition, the increased use of renewable energy had a positive 101 million metric tons of CO equivalents for 2021 (2020: 92 million 2 impact on specific greenhouse gas emissions. Since 1990, we have 2016 2017 2018 2019 2020 2021 metric tons of CO2 equivalents).3 We are continually working to been able to lower our overall greenhouse gas emissions from BASF reduce greenhouse gas emissions from our business activities – in operations by 49.7% and even reduce specific emissions by 75.4%. our own production and, together with our partners, along the value We are currently pursuing more than 250 technical and organiza- chain. As part of our carbon management, we aim to make our plants and tional measures to reduce energy consumption and increase com- processes even more efficient and resource saving. An important petitiveness. Our employees are an important source of optimization BASF was able to reduce emissions in the Scope 3 category component of this is the introduction and ongoing maintenance of ideas in this regard. For instance, suggestions for improvement sub- “customers” by 2 million metric tons in 2021, primarily through the certified energy management systems according to DIN EN ISO mitted by our employees in 2021 enabled us to avoid around use of new blowing agents in polyurethane (PU) foams. Until now, 2 These help us to identify and 12,000 metric tons of CO at the Ludwigshafen site in Germany alone. the main blowing agents used were hydrofluorocarbons. These are 50001 at all relevant production sites. 2 implement further potential for improvement in energy efficiency. used in the production of PU insulation materials to create foams This not only reduces greenhouse gas emissions and saves valuable We further improved energy and resource consumption in produc- with excellent insulation properties. The use of these hydrofluoro- energy resources but also increases our competitiveness. In 2021, tion with numerous projects around the world in 2021. At the Lud- carbons in PU products will be prohibited in the European Union 76 production sites worldwide had certified energy management wigshafen site in Germany, for example, a multi-stage evaporation from 2023 due to their high climate impact. We are therefore systems, representing 90% of our primary energy demand. system set up at one plant saves over 60,000 metric tons of steam gradually replacing them with hydrofluoroolefins, which have a much per year. At another plant, additional heat integration made it lower climate impact (measured by global warming potential, GWP). A global working group provides ongoing support to the sites and possible to supply other users with higher-pressure steam, reducing BASF began rolling out PU spray foams based on this new genera- Group companies in implementing and maintaining certified energy fuel consumption on the power plant side. At the Shanghai-Caojing tion of blowing agents on the European market back in 2017. By the management systems. All energy efficiency measures are recorded site in China, a modernized control concept reduced the fuel end of 2021, we will have almost completely converted our Eur opean in a global database, analyzed and made available to BASF sites as demand of a heat recovery unit, and at another plant, steam demand PU spray foam production and will continue to systematically drive best practices. was reduced by additional heat integration using a cooler. At the this forward in other regions as well. Geismar Verbund site in Louisiana, steam demand was reduced by the use of optimized condensate separators. In total, these mea- Our climate protection products offer our customers solutions to sures save more than 23,000 metric tons of CO2 annually. We also avoid greenhouse gas emissions over their entire life cycle com- achieved additional savings in steam, electricity and fuel through pared with reference products. The systematic analysis we conduct process improvements at many other sites. on our portfolio – Sustainable Solution Steering (see page 141) – 1 Sales product volumes include sales between BASF Group companies; merchandise is not taken into account. 2 Relevant sites are selected based on the amount of primary energy used and local energy prices. 3 Calculated in accordance with internationally recognized rules, including the use of values from general databases and industry averages.
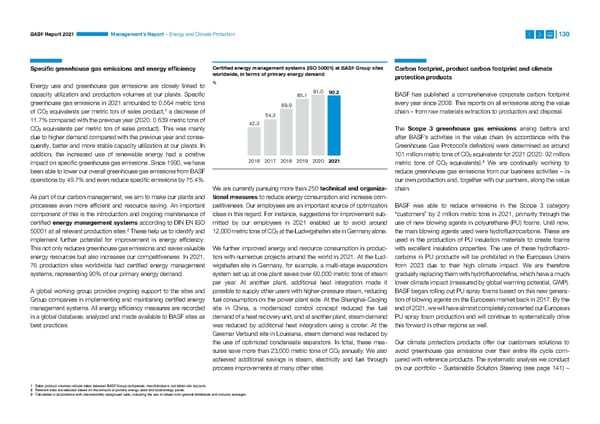